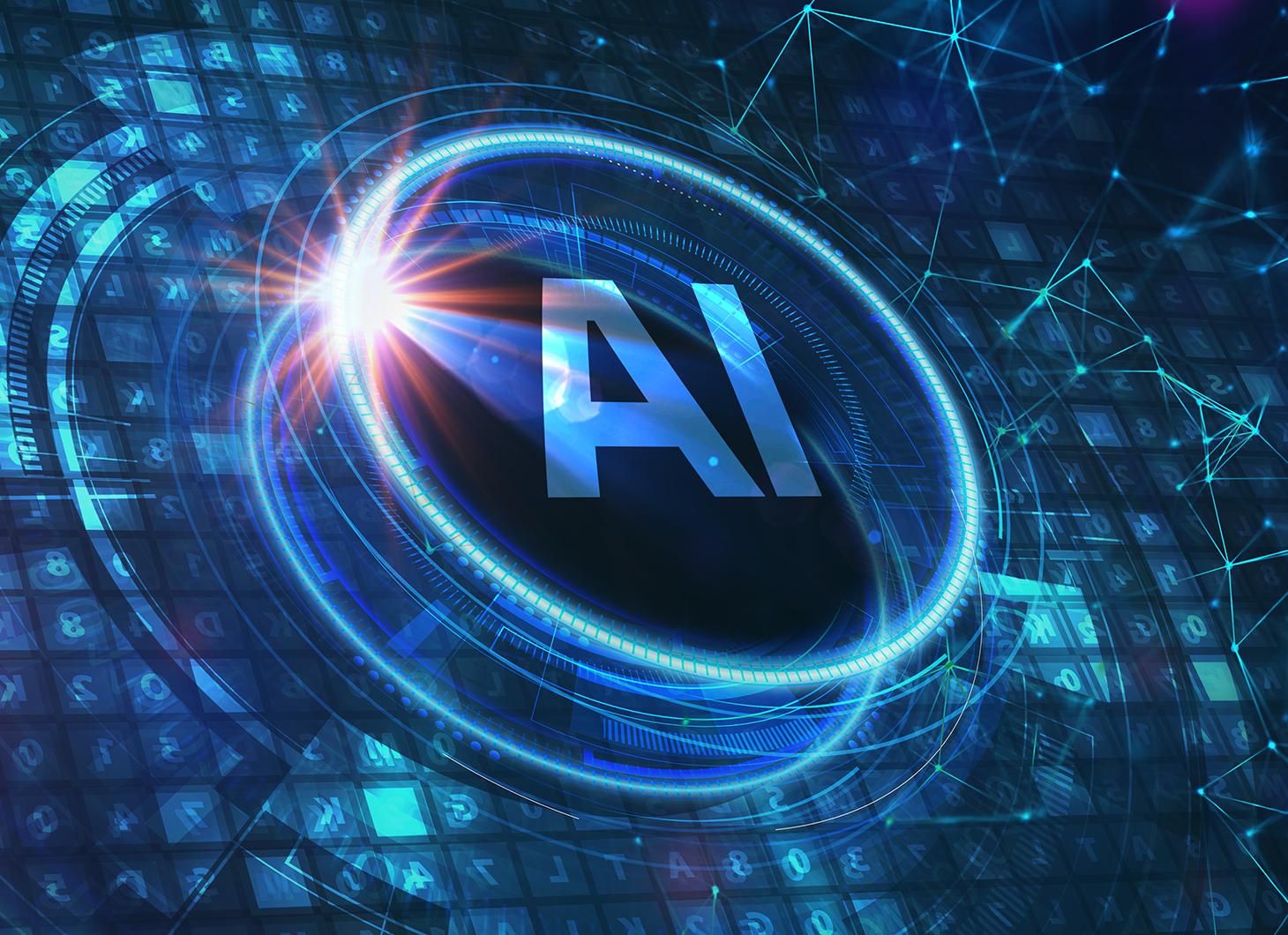
Artificial intelligence project provides tools for silicon wafer inspection – rare deviations can be detected even in larger data samples
The potential of artificial intelligence in the semiconductor industry is significant. In such a quality critical industry which processes microscopically small components, even the slightest improvement in quality assurance can bring great benefits.
– In addition to quality assurance, another characteristic use for artificial intelligence in the semiconductor industry is production control. It is a different branch in the development of artificial intelligence, and it can bring great benefits, says Tapani Alander, Product Development Engineer leading the artificial intelligence project at Okmetic.
Okmetic sought help from an EU project for the implementation of artificial intelligence
Okmetic has been involved in the Intelligent Reliability 4.0 (iRel40) project since May 2020, in which the reliability of electronics was developed by utilizing artificial intelligence in the entire electronics value chain. Many European research institutions, universities and companies in the semiconductor industry were involved in the large-scale project. The main focus is on automobile industry, but many other industries are also represented.
Okmetic aims to improve the process controls of its silicon wafer production during the project by using machine learning and artificial intelligence. Okmetic particularly focuses on improving the reliability of the bond interface of its C-SOI® wafers.
– We were offered an opportunity through the iRel40 project to test how artificial intelligence could help improve the reliability of our products and look closer what the industry leaders are developing at the moment. As soon as we are past testing, we can better identify the areas applicable to use of artificial intelligence, Alander states.
Implementation of artificial intelligence has been promising to Okmetic
Okmetic has now successfully completed a pilot, and artificial intelligence has been harnessed to alleviate the process engineering work. Since there has been no prior in-house experience in artificial intelligence, the project was started by obtaining in-depth expertise externally.
– Finnish SME “Labra AI” was chosen as our partner. Our tasks were to further refine the model to be more applicable to the production environment, as well as process training data. During last year, we had also recruited more people who had experience working with artificial intelligence, Alander says.
The purpose of artificial intelligence is to tirelessly go through data produced by the inspection equipment and notify the process engineer in case any deviating error patterns are detected.
– The inspection equipment can only inspect wafer chips individually, but artificial intelligence can also detect when patterns overlap chips. That generally means that the error is not sporadic but something deviating has likely happened to the wafer, Alander explains.
– When artificial intelligence performs basic tasks and inspects the huge amount of data created in production, the engineers can focus on more complex tasks, he continues.
The next goal in Okmetic’s project is to bring the first system into production by the end of the year.
– We have completed an implementation pilot, which helped us prove that the model works with real production data. Now we have to think how a real implementation into production will be carried out, Alander tells.
– When we compared the results of our pilot to other results of the same model, our results have been first-class in the world based on articles, he adds.
Will the use of artificial intelligence bring real benefit?
According to Alander, artificial intelligence is constantly vigilant in monitoring the measurement data of devices, and it can immediately detect if any error patterns start to show up in the results. Through quick reaction, the problem can be solved immediately and so the production of deviating products can be prevented.
– When using artificial intelligence, it is important to remember that it replaces a human in both good and bad. The good is that it can go through huge amounts of data fast and detect things that are mathematically hard to determine exactly. The bad is that even artificial intelligence makes wrong decisions: During the pilot, we noticed that over 95% of decision will be correct, but errors also occurred sporadically, Alander says.
– And since we are working in a reliability sensitive area, it is a significant problem, he adds.
During the pilot, it was detected that artificial intelligence detects deviating wafers extremely well, but it cannot always classify error patterns correctly. Instead of having an engineer to inspect each measurement separately, they can better focus on problem solving while assisted by artificial intelligence.
– Through this project, we have noticed everything that we can achieve at Okmetic with artificial intelligence – and how much effort it requires. We have had to invest in, for example, IT infrastructure, since artificial intelligence requires extremely heavy computational models, Alander tells.
– The assumption is that the reliability criteria of our customers will only increase across the board, Alander predicts.
At the moment, roughly one deviation in one million produced components is allowed for safety critical components. Self-driving cars will multiply the amount of critical electronics, and reliability requirements will also increase accordingly.
– We need to be able to detect small deviations in huge amounts of data even better than before. This is difficult to achieve without artificial intelligence systems, Alander emphasizes.